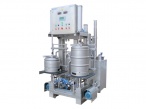
Purpose - Preparation for filling and filling keg-barrels with beer, kvass, wine, drinks (with a flat fitting)
Control mode - Automatic
Capacity - up to 30 KEG/h
Purpose of function
Cleaning and filling kegs (with flat fitting) with beer or kvass (mild rye beer); production capacity – up to 30 kegs/h.Operation mode
Automatic.Picture of the Unit
![]() |
![]() |
![]() |
Picture of a Keg-Tilter (optional device)
![]() |
![]() |
![]() |
Operation cycle sequence (position #1)
- Rinsing with hot water;
- Blowing-off with compressed air;
- Heat-up and cleaning with hot lye solution;
- Blowing-off with compressed air;
- Rinsing with hot water;
- Blowing-off with compressed air;
- Heat-up and cleaning with hot acid solution;
- Blowing-off with compressed air;
- Rinsing with hot water;
- Blowing-off with compressed air;
- Rinsing with cold water;
- Blowing-off with compressed air;
- Sterilization with steam;
- Blowing-off with CO2 (if required);
- Notching with CO2 (if required).
Operation cycle sequence (position #2)
- Blowing-off with CO2;
- Notching with CO2;
- Filling with product.
Video of the Unit in production
Unit configuration
The factory-assembled unit is mounted on a skid and comprises the following parts and blocks:- working bench with pneumatic clampers for kegs fixing;
- tanks heating elements for storage of lye and acid cleaning solutions;
- circulation pumps;
- electric switch cabinet, with PLC (by “OVEN-K”); operator’s touch-screen panel and pneumatic devices (by “SMC”);
- temperature and level transmitters;
- pipe connections, with valves, couplings and fittings.
Key technical features
Parameter Units |
Value |
---|---|
Production capacity (for kegs of 50L format), pcs/h |
up to 30 |
Number of working stations (heads position), pcs |
2 |
Hot water flow consumption (at pressure 3kg/cm2), max m3/h |
0.3 |
Cold water flow consumption (at pressure 3kg/cm2), max m3/h |
0.2 |
Steam water flow consumption (at pressure 3kg/cm2), max kg/h |
5 |
Compressed air consumption for pneumatic system (required compressed air purity as per GOST 17433, at pressure 6 kg/cm2), max m3/h |
1.5 |
Compressed air consumption for kegs blowing-off (required compressed air purity as per GOST 17433, at pressure 2.5 kg/cm2), max m3/h | 2.0 |
CO2 consumption (at pressure 2 kg/cm2), max m3/h |
5 |
Tank* capacity for lye cleaning solution**, max L | 140 |
Tank* capacity for acid cleaning solution**, max L |
140 |
Basic material of construction |
stainless steel AISI-304 (08Х18Н10) |
Ingress protection rate of switch cabinet |
IP 54 |
Total installed capacity, kW |
12.0 |
Power supply voltage, V |
380 |
Dimensions of the Unit, mm |
1510х1410х2200 |
Weight of the Unit, max kg |
440 |
Concentration of acid cleaning solution must not exceed 1.5%.
** - the tanks are not intended for dilution of concentrated lye or acid solutions.
Standard delivery terms
Scope of services:- Manufacturing of the Unit;
- Start-up and commissioning at the Customer’s site, with training course for the staff – by additional agreement with the Customer.
- Technical passport and manual;
- Declaration of correspondence to requirements of the Technical Regulations of the Customs Union (TRCU).
Guaranteed operating lifetime – 12 months.
IF YOU HAVE QUESTIONS, SET THEM TO US!